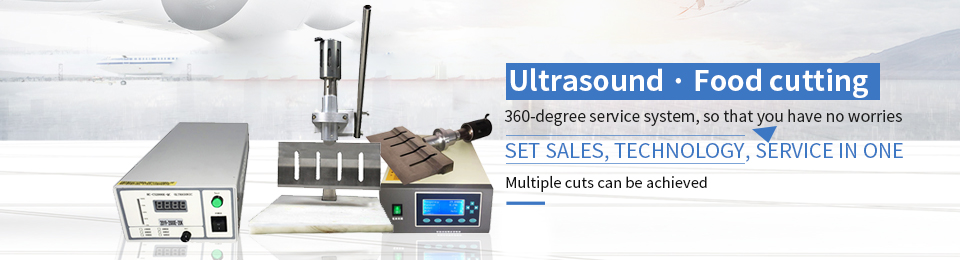
Tin plating and welding of ultrasonic soldering iron equipment
Traditional tin plating equipment usually uses corrosive flux to remove oxide layer or impurity on the surface more or less. In addition, it is impossible to weld materials such as glass, ceramic and aluminum with traditional tin plating equipment.
The new technology of ultrasonic driven welding joint does not need to add corrosive acid / flux. "Ultrasonic cavitation" cleans and removes oxides from the substrate surface on the molten solder during welding. Ultrasonic electric iron welding process, without flux, can realize welding of difficult welding materials and special base materials (such as glass, ceramics, aluminum, steel, titanium, silicon, metal oxide, superconductor) under atmospheric pressure. No flux is needed and the surface of base metal will not be corroded.
Equipment structure
Ultrasonic electric soldering iron equipment, whether hand-held or machine mounted, uses ultrasonic vibration heater iron tip to vibrate and melt solder layer. The piezoelectric crystal is installed in the handle of such equipment and connected with the metal tool head of the integrated welding head for longitudinal vibration. The tool head (solder head) usually passes through a heating tube or a resistance heating wire is wound around the soldering iron head. This design ensures that the tool head (solder joint) vibrates at ultrasonic frequency, usually between 20 and 60 kHz. Commercial equipment has a console, which can control the ultrasonic power (10 ~ 50W) and heating power supply, as well as temperature controller to control the temperature of solder joint.
working principle
In the process of ultrasonic electric iron welding, heat from a separate energy source melts the solder before the vibration energy is applied. Then, the molten solder is used as the acoustic transmission medium of ultrasonic vibration. When the high frequency vibration energy is applied to the molten solder, controlled acoustic cavitation is caused at the tip of the welding tool to destroy and disperse the surface oxide. Cavitation microbubbles break, clean all surfaces, wet the liquid solder and bond the pure metal.
High energy ultrasonic vibration produces cavitation in the liquid solder and removes the oxide film on the surface of the base metal to be welded. High pressure forces the liquid solder into the micro pores of the base metal, sealing these micro pores and making the surface of the base metal easier to weld. The bubbles in the liquid solder are extruded by ultrasonic vibration to realize the perfect welding without pores on the surface. The ultrasonic soldering process has good welding effect and high quality.
Welding characteristics
Ultrasonic soldering allows the joining of different materials and can be used for materials that are difficult to weld by conventional methods. Since no flux is required, users can save time and cost in cleaning flux residues, while reducing corrosion and improving the durability of welded joints. The ultrasonic soldering method can be easily carried out by hand with the help of hand-held ultrasonic electric soldering iron equipment, and can also be grafted to the ultrasonic welding machine and assembly line for use.
Development status
Ultrasonic soldering iron has been widely used in the welding of metals and ceramics, from solar photovoltaic and medical shape memory alloys to special electronic and sensor modules. This is a mature process and has been reported since 1955 as a method of welding aluminum and other metals without flux. With the "active welding ultrasonic soldering iron welding", the practicability of ultrasonic soldering iron welding technology is growing at a faster speed.
Application examples
Optical tin plated glass
Niobium coil wound to glass ceramic rod
Weld the titanium rod to the sapphire substrate
The copper wire is in electrical contact with the aluminum sheet on the glass substrate
Weld 120 μ m glass fiber into 0.5mm bronze hole
Contact ceramic carbon hybrid superconductor, welding point diameter 0.8mm
Solar cell contact: silicon silicon single crystal, thin film solar cell, dye-sensitized solar cell
Contactus
David wang
Hangzhou Dowell Ultrasonic Tech Co.,Ltd
Factory Add:No.8 Shengda RD,Fuyang District,Hangzhou,China
Office Add:No.107,Fengshou RD,Fuyang district,Hangzhou.China
TEL:86-571-87191379; +86-15088693503
wechat and whasapp:15088693503
FAX:86-571-87191379
Email:davidwang@dowellsonic.com
zip code:311400